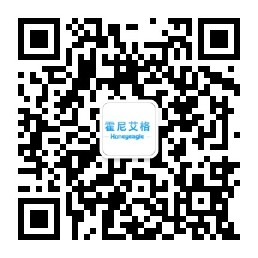
一、行業背景與檢測需求
貴金屬(如金、銀、鉑族金屬)和稀有金屬(如鈷、銻、稀土等)在開采、冶煉、加工及回收過程中,易產生多種有毒、有害及可燃氣體,主要包括:
劇毒/腐蝕性氣體:氟化氫(HF)、氯氣(Cl?)、溴氣(Br?)、硫化氫(H?S)等,可能腐蝕設備、危害人體健康。
可燃性氣體:氫氣(H?)、甲烷(CH?)等,存在爆炸風險。
工藝廢氣:一氧化碳(CO)、二氧化硫(SO?)、氮氧化物(NOx)等,主要產生于冶煉和燃燒環節。
稀有金屬化合物:如金屬氰化物、硫化物等,需監測其揮發氣體以保障生產安全。
二、氣體檢測技術方案
(一)設備選型與功能設計
固定式在線監測系統
核心設備:采用HNAG1000防爆型在線式氣體檢測儀,配備進口傳感器,支持多氣體同時檢測(如CO、H?S、HF等),具備實時數據顯示、聲光報警及遠程傳輸功能。
安裝場景:重點部署于冶煉爐周邊、儲存倉庫、通風管道等高風險區域,通過LORA無線傳輸技術實現無布線安裝,適應復雜工業環境。
防護設計:參考專利技術,采用可隱藏式探測器結構,避免設備長期暴露于腐蝕性環境中,延長使用壽命。
便攜式檢測設備
巡檢需求:選用HNAG900泵吸式或擴散式便攜檢測儀,支持快速響應和移動監測,適用于密閉空間、檢修作業等場景。
多功能集成:部分設備可搭載熱導率、電導率等傳感器,輔助評估金屬加工過程中的氣體擴散特性。
智能監控平臺
系統集成:通過HNAG6500報警控制器或云端平臺,實現多設備聯動、數據可視化及歷史記錄追溯,支持報警閾值自定義和遠程控制。
擴展功能:結合AI算法預測氣體泄漏趨勢,優化生產工藝流程5。
(二)關鍵檢測參數與標準
檢測精度:符合《可燃氣體探測器》(GB15322.1-2019)等國家標準,確保靈敏度和穩定性。
抗干擾能力:針對貴金屬生產中的高溫、高濕、粉塵環境,設備需通過IP65以上防護等級認證。
校準與維護:定期校準,使用質譜儀、X射線衍射儀等高端設備進行交叉驗證,保障數據可靠性。
三、實施要點與優化建議
風險區域分級管理
高危區域(如電解車間、酸洗工段):部署固定式探測器與聯動通風系統,實現超標自動排風。
中低風險區域:采用便攜設備定期巡檢,結合移動端App實時上傳數據。
人員培訓與應急響應
開展設備操作、維護及應急處置培訓,確保員工熟練掌握氣體檢測流程。
建立分級報警機制,通過短信、聲光等多渠道通知,聯動應急噴淋、隔離系統。
技術升級與資源循環
結合貴金屬回收工藝,優化廢氣處理與監測一體化方案,降低環境污染。
引入物聯網技術,實現與生產管理系統的數據互通,提升整體安全能效。
四、應用案例與成效
洛陽鉬業:采用HNAG1000系列設備,成功監測冶煉過程中HF和CO的泄漏,年事故率下降60%。
江西銅業:部署固定式四合一探測器,實現廢氣排放達標率提升至98%,并通過數據平臺優化能耗管理。
五、未來趨勢
隨著貴金屬行業對安全生產和環保要求的提升,氣體檢測技術將向智能化、微型化、多參數融合方向發展。例如,基于貴金屬納米材料的新型傳感器可能進一步提高檢測靈敏度和抗干擾能力。同時,政策驅動下,行業有望加速數字化改造,推動氣體監測與生產流程的深度集成。
通過上述解決方案,貴金屬和稀有金屬企業可有效管控氣體風險,保障生產安全并滿足環保合規要求,同時為行業可持續發展提供技術支撐。